record details.
interview date(s). | July 1, 2023 |
interviewer(s). | Galen Koch |
affiliation(s). | Haystack Mountain School of Crafts |
project(s). | Haystack Mountain School of Crafts Archive |
transcriber(s). | Galen Koch |
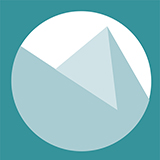
Since 2022, Haystack Mountain School of Crafts, an international craft school located in Deer Isle, Maine, has partnered with Maine Sound + Story to conduct interviews with individuals connected to the School—including those with both longtime and more recent relationships with Haystack, and whose participation with the School ranges from former and current faculty, program participants, trustees, and staff. Their voices and recollections help tell the story of Haystack.
This project is in partnership between Haystack Mountain School of Crafts and Maine Sound + Story, and was generously funded in part by Lissa Hunter, Ann Powers, and Claire Sanford, with grant support from the Maine Community Foundation’s Belvedere Traditional Handcrafts Fund and the Onion Foundation and additional operating support from Haystack Mountain School of Crafts and the Windgate Foundation.
Galen Koch: [00:00:00] Can you just tell me your name, where you’re from, and what you do when you’re not at Haystack Labs …?
Nicole Bakker: [00:00:32] Okay, So, my name is Nicole. I’m from the Netherlands originally, and I’m a student in the Center for Bits and Atoms [CBA] at MIT [Massachusetts Institute of Technology].
Galen Koch: [00:00:44] And what do you do at the Center for Bits and Atoms, usually?
Nicole Bakker: [00:00:49] I work on advanced biomaterials and sustainability. We’ve got a couple of projects in which that’s important. One of them is a shipping and fuels project. But we’re also looking at the metrology, being the measurement of materials, and I’m specifically focusing on the bio-based and recycled materials.
Galen Koch: [00:01:11] What are you working on here at Haystack Labs?
Nicole Bakker: [00:01:15] We have a very exciting project titled “Oyster Clay,” and we were interested in looking at the local biomaterials available. One of the things that Maine is very known for are oysters, and that’s why we decided to move forward with that as our primary material.
Galen Koch: [00:01:33] You were talking about the materials. Maine is really known for its oysters.
Nicole Bakker: [00:01:38] Yes. So, we used the oysters as a starting point to start experimenting with. At Haystack, you have all these beautiful studios with different themes, and in particular, the Clay Studio was a good place to settle in and start experimenting to make a clay-like material. So, that’s what we did.
Galen Koch: [00:02:01] How did you start that process? What was the beginning for you for that?
Nicole Bakker: [00:02:10] We actually went from raw oysters, and we had to grind them all down and then sieve them. There were many manual steps involved in getting those oysters to a fine particulate structure. So that took a while. There was a lot of manual labor involved, and we even had someone in the team build a custom-made grinder for it. That was really impressive. Some of the next steps were to use a ball-bearing machine – I think that was a wrong word.
Galen Koch: [00:02:47] A tumbler?
Nicole Bakker: [00:02:48] Yeah, a ball tumbler. No, a ball – yeah, something like that.
Galen Koch: [00:02:55] I don’t know what it’s called, but we’ll figure it out.
Nicole Bakker: [00:02:58] So we used that ball roll thingy [ball mill] for grinding the materials, and then we mixed it in a variety of substances … After grinding the material down at a very fine level, we then made different mixtures with additives, and made a taxonomy of materials to see what each additive would factor in and how that would change the final product.
Galen Koch: [00:03:33] What kind of things were you using, were you experimenting with?
Nicole Bakker: [00:03:37] One of the things that we put in there was honey, and that might actually attract these animals right now [laughter] because we’re still working with it. That was one. We worked with glycerin as a plasticizer, we worked with a little bit of eggshells, and we worked with bentonite. So, we have a few different materials that we experiment with to get a good paste, basically. The ultimate goal is to 3D print with it.
Galen Koch: [00:04:09] Wow. When you are working with – creating this material, what sort of properties does it need to have to be able to be 3D printed? What are you looking for?
Nicole Bakker: [00:04:22] For 3D printing, clay needs to have certain properties. An important one is the rheology, and that’s basically to make it easy to go out of the nozzle because it’s a very thin nozzle, so you need to be able to have the flow in the right way. If your material is too watery, then it will basically just fall out, and there will be no structure that will stand up. If it’s too dense, then it will not come out, and we’ll clog the nozzle. So, there’s a few parameters that are really important. The most important one is rheology and then, of course, also the particle size. If the particles are too big, then it can actually break parts inside or get blocked or cause all kinds of problems. So those are two specific factors to look at. There’s, of course, more if you go deeper into this, but these are the main materials and properties you have to look out for. In general, with biomaterials experimentation, you, of course, push these machines to the limit and really try and do all kinds of crazy experimentation. So you always want to make sure to clean very well afterward, because otherwise, it’s going to get contaminated or you mess up the next experiment.
Galen Koch: [00:05:56] Through this process, do you feel like you are experimenting in a way that you’re going to take something back to the lab when you leave or to your research?
Nicole Bakker: [00:06:10] Yeah. I think we’ve met a lot of amazing people. This whole experience here of being in these different labs and having people from all different disciplines, bringing them together, that’s been really inspiring to me. Because if you work on a certain property of a material and you try to get it better, then there’s, I don’t know, a physicist or material science scientist coming in or someone who is a ceramicist – everybody brings in their own perspectives and their own experience. That combined experience has been extremely helpful in this project and, I think, in many other projects as well. Having this interdisciplinary collaboration is something that I’ll seek out in my research more after this.
Galen Koch: [00:06:54] Is that sort of a new discovery for you, something that you want to seek out?
Nicole Bakker: [00:07:01] It is actually something that I’ve experienced before in programs where I bring people together in an interdisciplinary environment. Yet, I think particularly here at Haystack, because we have such a short amount of time, that time compresses innovation. Being in a natural environment and sort of relaxing, you don’t have to think about anything else except your research. I think those are the circumstances that create this pressure vessel for these things to actually happen instead of only happening on paper or in theory for people to work together. I think that’s really powerful about being here, specifically at Haystack.
Galen Koch: [00:07:40] Yeah, that’s so amazing to think about the time compression as a component of – it’s one of the ingredients that makes it all work.
Nicole Bakker: [00:07:51] Yeah. Not only that, because sometimes the pressure can be intense, but because this is in such a beautiful environment and very calming – you can go to the beach, you can go to the woods and just relax together. That makes it a well-curated pressurized experience.
Galen Koch: [00:08:10] Had you been to Haystack Labs before?
Nicole Bakker: [00:08:13] No. This is my first time.
Galen Koch: [00:08:15] That’s great.
Galen Koch: [00:08:17] Can you just show me, like, with this? What? I don’t want to mess it up. [Points at biomaterials samples.]
Nicole Bakker: [00:08:23] Yeah, I can come get it.
Galen Koch: [00:08:24] Here, I can – I might be able to pass it to you.
Nicole Bakker: [00:08:27] Yeah, absolutely.
Galen Koch: [00:08:33] So this, I assume, is the different additives.
Nicole Bakker: [00:08:36] Yeah, here are the additives. There’s a little bug on it. How far can you see it?
Galen Koch: [00:08:47] I can see it in your lap. If you just want to describe it.
Nicole Bakker: [00:08:51] Wonderful. So, honestly, this is a very nonscientific way of exploration because we’re in an art place here, so that’s why we were basically playing around with the materials and shutting off our scientific mind a little bit. But we did do some validation before we started mixing these materials together because that’s always a good way to start. I think that’s also a recommendation for artists here. If you’re interested in exploring biomaterials, this is kind of the first step that you do. We thermoformed a container so that you can present the results nicely. There’s a beautiful new thermoformer in your lab here as well – in the Fab Lab – so you can make this as well. This is the alginate with oyster. So, we mixed the oyster with water and alginate.
Galen Koch: [00:09:42] One moment, I’m going to switch over my SD card. I’m so sorry.
Nicole Bakker: [00:09:45] Oh, okay. No worries. [RECORDING PAUSED] All right. So, on this side, you see the oyster combined with alginate used as a binder. There are different types of binders that you could use, and we decided to go for alginate this time. But there’s a broad variety of other materials that you could explore. This is four slots with exactly the same composition, and we just put it there to test how different drying processes would come out. The rest, however, is with the additives. So this is the oyster with the bentonite and alginate. Here, it starts for all of them. It starts with a little bit, like one scoop of the material, then one more scoop, and then more, and then a lot to see the progression of how much of the material mixture would change the final output of the product. The second is oyster with honey and alginate, so we put honey in there, and that actually gives a pretty nice structure, so it’s pretty soft, and it’s getting more viscous, which is a property, of course, that honey has. The next one has glycerin in it that’s also used as a plasticizer. It’s also edible. The last one is with eggshells; we put eggshells in there. So here, for example, with the bentonite, you see cracks. This one dries way faster. Right now, because we are limited in time, we decided to put it out in the sun to dry. That’s why some of the cracking happens. You can also experiment with ways you can dry it. There’s many different forms and methods in how you can process it, which will influence the outcome. That’s what we did.
Galen Koch: [00:11:40] That’s so cool. The honey looks really good.
Nicole Bakker: [00:11:45] Yeah, I think the honey looks really good.
Galen Koch: [00:11:48] What’s your hope for –? What are you working on for the rest of your time? Are you actually going to try the 3D printing?
Nicole Bakker: [00:12:02] Yeah. At the moment, we are loading the 3D printer with the mixture that we settled on. So it’s going to be a very interesting moment to witness that when a 3D printer is going to do that operation. It’s like a final graduation of this project, and we’re very excited to see that come to life.
Galen Koch: [00:12:27] I interviewed Dana, who’s in the clay studio. It sounded like she’s excited about these materials and sneakers and footwear. For you, do the oysters go beyond –? Could the material be used for something, or is it more about you just thinking about processes and doing things in a different way?
Nicole Bakker: [00:13:02] Personally, I’m very interested in the broader impact of biomaterials, bio-based materials, recycled materials on the global economy, and there is a big movement towards that. So this is really a contribution in getting there. We are so reliant on fossil fuels for our plastics, for our fuels, for all of that, that there’s a growing need to be able to create new materials that fulfill the needs we have as humanity and look for alternatives that don’t pollute the Earth so much. This is one step. The Oyster Project is one step in achieving that goal. But I’m also exploring more materials. So, I’m basically neutral to the type of material that I use. I’m mostly interested in looking at what is local and what can local people do to upcycle their materials so that you don’t even have to buy from the global supply chains.
Galen Koch: [00:14:03] That’s amazing. You do work with shipping.
Nicole Bakker: [00:14:08] Yeah.
Galen Koch: [00:14:09] Wild. Yeah.
Nicole Bakker: [00:14:11] So, I mean, we have a lot of different projects at CBA, and I also worked – so, before coming to CBA, I started a company. I worked with many different industrial manufacturing companies – aviation, even a Formula E racing team, and they all wanted to make their materials more bio-based and sustainable. So, this is not only something that’s interesting to artists or makers or designers, but also, actually, big companies are also looking for solutions for their materials because they have to become more sustainable as an organization. Whatever the motivation is, we all have to do it right now. So, there is an emergent need for designers, artists, and makers who are enabling this transition.
Galen Koch: [00:15:01] Yeah, that’s so great. I know you want to get back, but is there anything else that you wanted to say about Haystack Labs or the work you did here?
Nicole Bakker: [00:15:11] I just really want to thank everyone at Haystack for enabling this beautiful experience. It’s been absolutely wonderful to meet and connect with like-minded people and to be inspired by such genius minds and the people at Haystack. I feel like this whole environment is just created with so much intention and inspiration that I think it’s really taking the inspiration to our lab beyond this Haystack experience. I really want to thank you all for providing this week to us.
Galen Koch: [00:15:44] Oh, thank you so much. That’s so great.
This interview features Nicole Bakker, a Center for Bits and Atoms student at MIT, discussing her work on biomaterials and sustainability. She highlights her participation in the Oyster Clay project, an exploration of using local biomaterials, specifically oysters, to create a clay-like substance for potential 3D printing. The interview delves into the experimental process, the significance of interdisciplinary collaboration, and the broader impact of bio-based materials on global sustainability efforts.