record details.
interview date(s). | July 5, 2022 |
interviewer(s). | Galen Koch |
affiliation(s). | Haystack Mountain School of Crafts |
project(s). | Haystack Mountain School of Crafts Archive |
transcriber(s). | Galen Koch |
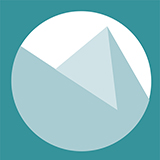
Since 2022, Haystack Mountain School of Crafts, an international craft school located in Deer Isle, Maine, has partnered with Maine Sound + Story to conduct interviews with individuals connected to the School—including those with both longtime and more recent relationships with Haystack, and whose participation with the School ranges from former and current faculty, program participants, trustees, and staff. Their voices and recollections help tell the story of Haystack.
This project is in partnership between Haystack Mountain School of Crafts and Maine Sound + Story, and was generously funded in part by Lissa Hunter, Ann Powers, and Claire Sanford, with grant support from the Maine Community Foundation’s Belvedere Traditional Handcrafts Fund and the Onion Foundation and additional operating support from Haystack Mountain School of Crafts and the Windgate Foundation.
Sigrídur Helga Hauksdóttir: [0:00:14] My name is Sigrídur Helga Hauksdóttir called Sigga or Sigga-Helga, and I’m from Iceland. I studied art in Iceland and design in the UK, where I lived for ten years. And I’ve been making all kinds of things.
Galen Koch: [0:00:38] Like what? What sort of things? What do you work in, and what do you dabble in? It sounds like all kinds of things.
SHH: [0:00:45] Yeah, it does. The thing is that I find materials exciting in themselves and processes as well. So, working in ceramics and mold making is one thing, and then silver and silversmithing and casting and stuff like that. And glass and glassblowing and woodwork. So yeah, the materials, in general, I do find exciting.
GK: [0:01:16] When did you start to become involved in a Fab Lab?
SHH: [0:01:23] So that was 2014. We were asked back in Fab Lab Reykjavik to come and teach some students, and basically, we knew nothing. We had to figure out a way of learning, and we asked around if there was some course or anything we could take, and we were pointed to the Fab Academy. So, we took a course that was like a six-month course or something? Twenty weeks. I don’t know. That was pretty intense, but we learned how to use the lab, so we then felt excited about incorporating that into our own work. And me and Margrét [Óskarsdóttir] have a sort of artist alter ego called Sigmar, which is an anagram from our names, and that artist has been making a lot of sculptures and stuff in the Fab Lab where we combined our strengths in there.
GK: [0:02:27] When you started that Fab Academy course, how were you thinking that you were going to interact with the machines? Were you daunted? Was it intimidating? Or were you immediately kind of thinking, “Oh, we’ll integrate this into our work?”
SHH: [0:02:44] Yeah, yeah. It was more an integration. In the Academy, there are different things that you’re taught, like programming and making motherboards, and that was totally well out of my comfort zone and utterly new to me. But I’d been designing in all kinds of software before, so I did have to brush up on some of those skills, but that came sort of more natural. Also, having background in mold making, thinking in positive and negatives, and working a lot with vector graphics and stuff like that and images.
GK: [0:03:33] You had some experience with that before.
SHH: [0:03:35] Yeah. Yeah.
GK: [0:03:37] And how did you end up at Haystack?
SHH: [0:03:41] That was during a session in the Fab Academy where we would be picked on, I would say. You would be asked to present your work and during that time, Neil [Gershenfeld] suggested Haystack. He suggested it and made it happen for us or passed our names along, and we were invited. So, that was great.
GK: [0:04:11] How many sessions was that for? How many years have you been coming?
SHH: [0:04:16] 2016, we came for two sessions. 2018, we came for the one session. And back in 2020, we were asked to come again, and that again got postponed until ’22.
GK: [0:04:31] We lost a couple years. When you came to Haystack, what was that experience like the first time for you?
SHH: [0:04:43] It was awesome. It’s like being with like-minded people that are working in this kind of different materials, and it’s problem-solving in the Fab Lab with all kinds of different processes and methods. Since I’ve dabbled in a lot of those, I kind of have an understanding of what they’re trying to achieve. I find it pushes my thinking about how I would approach the machines, as well. So, finding solutions – sometimes Fab Lab is not the answer to the question, and that’s also good to know that, that well, it’s so simple to make another way rather than having to go through the time-consuming process of making it digitally.
GK: [0:05:38] Yeah. What are some of the best examples of work that you think is really great to integrate with the Fab Lab?
SHH: [0:05:51] I see the Fab Lab as just a bunch of tools. You can have hammer and chisel, and that would do a great job for certain materials. Then, a pencil is a tool. And then the Epson printer that you have at home and you print out your photos; that’s also a tool. And this is just another sort of toolset that you can have. It’s always appropriate to find the right tool for the job you’re trying to make. At the beginning, there was a lot of novelty making; people just found the machines themselves fascinating, but I think people are now approaching it more as to how can they help me make something really quick that will support my work another way.
GK: [0:06:48] When someone comes in with an idea that you’re like, “I’m not sure if this is the Fab Lab application,” is that simply just because there might be a better tool? That’s how you think of it?
SHH: [0:07:01] Yeah, or better method of fabrication.
GK: [0:07:07] Working with the students here, has that changed your own process of making at all?
SHH: [0:07:15] Yeah, we’ve been influenced by a lot of people that are coming in. We’ve had a sort of exchange of knowledge. A good example – milling and plaster. I’d never done that before. Here was a student that came in with that kind of – he had done that before back home. And so, for me, it was a challenge to do that kind of thing. Also, just meeting all the artists that are here – that’s also very inspiring. This is such a creative hot pot. Everything is sort of bubbling, and people are generous with sharing, so you learn new techniques. Something that has influenced our work is the Japanese method of burning the wood. We’ve been making wood sculptures, and now we’re experimenting with burning the surface of them and blackening it. Something we picked up here at Haystack.
GK: [0:08:21] Wow, that’s amazing. Then, you would take something that you might learn in a session and just go for it on your own for a long time.
SHH: [0:08:29] Yeah, yeah.
GK: [0:08:31] In this session, are there any examples of a really great, successful integration between the studios and the Fab Lab?
SHH: [0:08:44] Oh, yeah. I think people have been coming in – for example, now they’re making huge, big sculptures in ceramics. One is making data-based circles, which she’s then cutting out and making a big sculpture. So that helps her to cut out accurately. So, she’s working with those ideas.
GK: Can you take me through the process of that? So, when someone for that specific project –? Did that student come in and chat with you? And then you say, “Okay, this is what I think you should do?” How does the process work?
SHH: [0:09:36] In this case, the person should have had a rough idea what they wanted to do. They had collected the data and converted them to circles. She had been doing some drawings and 2D work already with that, and now she wanted to translate that into a 3D piece. So, she took the circles and then cut them out of plywood, and the plywood would be the structure.
GK: [0:10:09] And then clay goes on top of that?
SHH: [0:10:11] Yeah. It’s just a support to keep the proportions right.
GK: [0:10:17] Wow. I hope we can see that, but I don’t know.
SHH: [0:10:21] Yeah, I don’t know. I was looking. The model itself might be destroyed already. Something is probably in the kiln, but the mold – the cast from it is there. I saw that earlier.
GK: [0:10:36] So, the plywood and those concentric circles, that was the mold, basically?
SHH: [0:10:45] Yeah, that was the model. The model then took a mold from it, and now they’re [inaudible] building into the molds, the press molds.
GK: [0:11:01] So when you are working as a resident in the Fab Lab, it sounds like you have … the technical skills that you need, right? You have to have technical skills. But then there’s this added layer of understanding, like you said, that there’s a mold and then the casts from the mold, and there’s this negative image and a positive image. Can you just talk about some of the different skills that you need to be a resident here?
SHH: [0:11:44] I think anything flies. I think people could just bring in what they already have. For us, we are not programmers, and that may be our weakness. If there were somebody who would like to program something with scale, do something – there was a weaver who wanted to weave with copper and make it interactive, and we were like, “Oof.” [laughter] We could do it. But then she would be our only client the whole session. I think skills needed are probably quite a lot of drawing in vectors programs and 3D programs and the machining.
GK: [0:12:38] And the machining. I mean, for me it seems it feels intimidating. Right?
SHH: [0:12:44] It can be, yeah. [laughter]
GK: [0:12:45] Can be intimidating. How has learning the machining been for you personally as an artist? What has that given you?
SHH: [0:12:56] I like challenge. [laughter] It has been just a way to expand the process. I do a lot of photography, and it has been a nice way to take the photography back into a 3D form, which I find exciting. So, with height mapping and stuff like that. The machining can be – so, we work as a team, and we have a bit of a role, so I do the computing and the settings in the computer, and Margrét is more on the machine. But still, when I finish my file, I go, “Margrét, come over here and see. Is that correct? Is that correct? Do you agree with that and so forth?” And she does the same to me on the machine. So, when I come over, she’s like, “Is everything correct? Is this what we’re supposed to be doing?” We’re a pair of eyes and two brains – that helps, especially with the ShopBot, if you’re doing a lot of 3D milling that is complicated.
GK: [0:14:05] Is your experience in the Haystack Fab Lab different than some of the other fab labs that you’ve been in?
SHH: [0:14:12] Oh, yeah. There’s a lot more exciting equipment. [laughter] There is equipment here that we don’t have. There’s one that we’re still hoping to try out, which is the plasma cutter. But we will have to see. There might be a class coming in tomorrow to have a look at the plasma cutter.
GK: [0:14:40] The plasma cutter? Whoa. What does that do?
SHH: [0:14:43] Cut metal. Steel.
GK: [0:14:46] Okay. Plasma like blood? No.
SHH: [0:14:51] I hope I’m saying it right. I think it’s called plasma cutter.
GK: [0:14:54] Yeah. When you’re in other – I mean, there’s a fab lab in Reykjavik that you work – do you work in that?
SHH: [0:15:03] No.
GK: [0:15:04] You just use it?
SHH: [0:15:05] We used to use it a lot in the sense that we would bring groups of students to the lab, but we would then always prepare our students back home, maybe have a little visit, get them acquainted with machines, come back, do some designing, and then come go back. Now, there has been a lot of scheduling conflicts with the lab, so we will have to make another arrangement. So we actually have a 3D printer, vinyl cutter, and a laser cutter at our school, which is kind of what a lot of schools have already acquired, so we use that to teach those student groups. But at the Fab Lab Reykjavik, we have been giving some courses for teachers to teach them how to use it and how to incorporate that technology into the teaching. We’ve also been giving some ShopBot courses, so that’s our Fab Lab Reykjavik connection.
GK: [0:16:04] I just ask because I wonder how the use of this Fab Lab differs from a Fab Lab like that one. Is Haystack unique in any way? The way that you function as a resident here or the interactions with students?
SHH: [0:16:25] I think the projects here – these are all artists coming from all over in all different fields. They come in with different problems than you would maybe see on an average day in Fab Lab Reykjavik. [laughter] Either people are intimidated by it and don’t come, and I’m talking back home, and then they just stay away, or they come up with crazy ideas. Here, you have more crazy ideas, so it pushes the lab to its limit.
GK: [0:16:59] Do you have any favorite projects from over the years? You mentioned Japanese wood burning as something that influenced you. Do you have other projects that really stand out in your mind?
SHH: [0:17:12] Oh, let me think. There have been many. For now, I think I’m really excited about the scanning possibilities with our new scanner we have. I don’t know. What project stood out? I don’t know. They all do in a way because they are all sort of part of the process. But I like to think that normally, there is not a final product made here; it’s just support towards the final product.
GK: [0:17:44] It’s just one piece in the process.
SHH: [0:17:46] Yeah. It’s just like another hammer you can use. [laugher] Whether a hammer is always appropriate, I don’t know.
GK: [0:17:58] What’s the scanner? If I get footage of that, can you tell me what is so exciting about that scanner for you?
SHH: [0:18:07] For me – well, we’ve done quite a bit of scanning with our own work, and it’s always been so problematic getting it to be accurate. We’ve even tried the needle scanner, which takes overnight trying to pinpoint everything, but this one got it pretty accurately just by running a few times on the revolver disk.
GK: [0:18:31] And it’s a 3D scanner. Is that what it is?
SHH: [0:18:34] Yeah, but we are still figuring it out. It made a complete and utter replica of the object that we had on there. So, I was impressed. [laughter]
GK: [0:18:45] It’s kind of space age. Wow. It’s pretty amazing.
SHH: [0:18:50] Yeah. In our work, our own personal artwork, we like to go backwards and forwards. So, for example, we make paintings, then we might take a photograph of the painting, and then we might height map it. We might mill the painting, then paint over it again. So it’s like a layered process. Or we might burn it – burnish it and make it black and then paint over it. We like that process of going backwards and forwards in the process and using the technology as something that influences us.
GK: [0:19:24] Yeah, I think that seems to be a really wonderful application for this kind of technology and something that people are really doing here at Haystack.
SHH: [0:19:35] Yeah.
GK: [0:19:36] Do you want to continue coming to Haystack?
SHH: [0:19:40] I would love to. I would love to. This is like heaven on earth. This is such a great place, the whole culture around it.
GK: [0:19:53] Are you working on work yourself right now, here?
SHH: [0:19:56] Yeah, we’re trying. [laughter] We got given a lot of nice hardwood that was unexpected back in Boston. So, we’re trying to make a few pieces, just the test pieces.
GK: [0:20:13] So, what does that look like? When you’re a resident here in the Fab Lab, what does your typical day look like? When do you find the time to work on things?
SHH: [0:20:26] Evenings. There’s a lot of late-nighters [laughter] and the weekend. Since we arrived on a Saturday and we had the whole of Sunday to work on our own, we took the Monday to acquaint ourselves with all the machines. But still, we had a few students come in, even though it’s officially not open yet. But since all the other faculty and teachers and all the other students are actually giving good presentation of their own, some of the teachers were coming in and using it and making stuff for the faculty.
GK: [0:21:06] You introduce the Fab Lab first to the faculty, right? Is there a way that you talk about it – do you feel like you’re talking about it in a certain way to engage them?
SHH: [0:21:21] Yeah.
GK: [0:21:22] And what is that?
SHH: [0:21:23] I think it’s important that this is a safe space to experiment. And also, I think a good thing is to realize that we are not making things for people but with people, helping people. Also, just to point out the possibilities, what can be done. Often, they are thinking [of] a certain printmaking thing, and then we can point out, “Oh yeah, and you can do that and that and that. Well, that’s a possibility,” and so forth.
GK: [0:22:00] I like that idea of you’re making things with people, so it really is collaborative.
SHH: [0:22:08] Yeah. Some people only need very little assistance. A lot of people have now experience with those kinds of machines, the lasers, and stuff. It’s in most colleges now, so a lot of those young people just design by themselves, sign up for the laser, do this stuff, and they’re off. But in other cases, it’s more of problem-solving with finding out what can be done, how it should be done, what’s the best tool, and what’s the best process. For example, one wanted to make a big wooden pyramid, but it had to be out of solid wood, and it turned out like old fashioned regular tools were the best. That was not suited for the Fab Lab. So you have to know when it’s appropriate to use it.
GK: [0:22:59] And that seems like that’s something that you kind of need a resident to know. That would be your expertise; you can say, “Here are the tools, and I think you could use this.” You are so knowledgeable in many materials you probably have knowledge beyond just what’s in the Fab Lab.
SHH: [0:23:23]Yeah. I used to teach mold making at the uni [university] back home, and we’ve been teaching silversmithing ourselves. We’ve been teaching printmaking ourselves. We’ve been doing woodworking as well. I know the processes, what they are going through. Our attitude is always, let’s say yes to everything, and let’s try to figure it out. I always like a challenge, but it has to be a realistic one and not to be selfish and say, “Yes, just because I find it exciting.” It would take them a long time to make it in the Fab Lab rather than point them in the right direction.
The interview conducted by Galen Koch with Sigrídur Helga Hauksdóttir provides insights into Sigrídur’s background in art and design, her involvement in the Fab Lab Reykjavik, and her experiences at the Haystack Mountain School of Crafts. Sigrídur, also known as Sigga or Sigga-Helga, hails from Iceland and has studied art in Iceland and design in the UK. She has a diverse range of skills, including ceramics, mold making, silversmithing, glassblowing, and woodwork. Her involvement in the Fab Lab Reykjavik and the Fab Academy course led her to integrate new technologies into her work despite some initial challenges. Sigrídur’s experiences at the Haystack Mountain School of Crafts have been transformative, with her participation in multiple sessions and her role as a resident in the Fab Lab. She highlights the unique and diverse projects undertaken at Haystack, emphasizing the collaborative and supportive environment that encourages artists to explore new ideas and push the boundaries of the Fab Lab’s capabilities. Sigrídur’s expertise and willingness to take on challenges have made her a valuable resource for both faculty and students, and she expresses a strong desire to continue her involvement with the Haystack Mountain School of Crafts.