record details.
interview date(s). | July 1, 2023 |
interviewer(s). | Galen Koch |
affiliation(s). | Haystack Mountain School of Crafts |
project(s). | Haystack Mountain School of Crafts Archive |
transcriber(s). | Galen Koch |
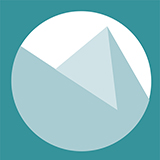
Since 2022, Haystack Mountain School of Crafts, an international craft school located in Deer Isle, Maine, has partnered with Maine Sound + Story to conduct interviews with individuals connected to the School—including those with both longtime and more recent relationships with Haystack, and whose participation with the School ranges from former and current faculty, program participants, trustees, and staff. Their voices and recollections help tell the story of Haystack.
This project is in partnership between Haystack Mountain School of Crafts and Maine Sound + Story, and was generously funded in part by Lissa Hunter, Ann Powers, and Claire Sanford, with grant support from the Maine Community Foundation’s Belvedere Traditional Handcrafts Fund and the Onion Foundation and additional operating support from Haystack Mountain School of Crafts and the Windgate Foundation.
Galen Koch: [0:00:00] Okay, so to start, tell me who you are, your name, where you’re from, and what you do when you’re not at Haystack Labs.
Dana Maringo: [0:00:09] Sure. I’m Dana Maringo, and I currently live in Portland, Maine. I’m originally from Pennsylvania. I work as a computational designer at the shoe company New Balance. I work mostly on performance footwear and how we can incorporate more meaningful data-driven designs into footwear. I also help designers create workflows and incorporate new technologies into their design tools.
GK: [0:00:38] Wow. Can you just tell me what computational design is?
DM: [0:00:43] Sure. Yeah. It’s designing with an algorithmic mindset; some people use the term generative or parametric design. So, it’s all in the same genre. It encompasses a wide variety of facets. We’re able to do visualizations; we visualize data in different ways. We create form and geometry from data, and we’re able to then incorporate that into products and actual footwear designs.
GK: [0:01:21] Wow. And what have you been doing at Haystack Labs?
DM: [0:01:24] Yeah. So, I’ve worked a lot with 3D printing at New Balance, and so I was really interested in the ceramic 3D printer that I heard about. I jumped on that project and started collaborating with a few people, thinking about how we can use these new artificial intelligence tools with design workflows. You can create images with these new tools from either text prompts or blending of different images, so we’ve been looking into that at New Balance. I was interested in creating a 3D object from an AI-generated image, so that’s what I did. I printed a series of four different cylinders with these very abstract images on them. I was looking at how you can understand the resolution of the printer and the textures and the forms you can get with these very high-resolution images.
GK: [0:02:26] Is that a departure for you in terms of material or process?
DM: [0:02:32] Yes, it is. Not process, exactly, because I think we’re always looking at new ways to design and how to incorporate certain aspects that are either functional or material-driven into the design process. So, the material is completely different from what I’m used to working with, which is actually pretty refreshing because it’s more of a crafted, hands-on type of tactile material. I’m used to working with very high-performing materials: a lot of plastics, foams, rubber and things like that.
GK: [0:03:17] Is it informing your work in any way, do you feel like, your time at Haystack Labs?
DM: [0:03:23] Yeah, I actually think the most valuable part for me so far has been really trying to understand what other people – what their goals are and what their challenges are, especially on the design side. Working with the artists that are here, explaining what I do and hearing from them the things that they’re pulling out and what seems most important to them. So, overlapping, how can I help you, and how can you help me? It’s been a lot of running around and helping each other on little aspects to get the project made or to come up with the end result of producing something. I think it’s been extremely valuable.
GK: [0:04:16] How did you end up at Haystack Labs? What was the story?
DM: [0:04:22] The story was I ended up connecting with James [Rutter]. I was really interested in being involved here. I was thinking maybe as a resident artist and pursuing personal work. But I was also really interested in potentially being involved in a new workshop and how we could help people who are interested in either footwear design or something else just based on the design tools that we use. The conversations were going, and then James invited me to join, and I’m very grateful. I wasn’t in touch with anyone prior, so I’m coming in without working with a lot of the MIT [Massachusetts Institute of Technology] people that are here, but it’s been really fascinating to see everything that’s going on here.
GK: [0:05:19] Yeah, it sounds like – so, one thing for you that’s been really just a great part of the experience is the network of people that’s here. Can you talk more about that? Who is it? What are the conversations that are happening for you?
DM: [0:05:35] Yeah. From my perspective, a core component of the group is from the MIT Center for Bits and Atoms, a lot of PhD students, a lot of post-docs, a lot of machine builders and programmers. I find that I’m at the intersection between that very techie space and the artist space. I identify more with the designers and the artists than the coders, but it’s a really fun place to be. I think having the juxtaposition of all of these different types of backgrounds and interests really makes it come alive. Everyone is bringing different strengths, so it feels like we can really make anything here.
GK: [0:06:37] And people are making anything.
DM: [0:06:39] Yeah. [laughter]
GK: [0:06:42] So, in the clay studio you were building – walk me through. You were making objects with machines.
DM: [0:06:54]Yeah.
GK: [0:06:55] I saw a big arm thing in there, too.
DM: [0:06:59] So those are robotic arms that can be hooked up to a clay extruder. I wasn’t working on that, personally, but I was working on the WASP 3D printer. There’s another person here who came from that company who’s been running and facilitating and helping everybody troubleshoot their designs and get everything printed. That’s been really interesting for me to learn a new material in the same technology. It’s been cool. I also started – I learned the vacuum former as well. So, I started vacuum-forming shoes and thinking about ways that we could use those molds for potentially repairing footwear, empowering people to seek that out and keep shoes for longer. Also, I forgot to mention I inserted myself into the biomaterials exploration because I’m really fascinated by natural materials, especially in the industry right now; even though there’s incremental change on the sustainability front, there’s a huge push to improve materials and processes and manufacturing methods. So, I got really dirty grinding oyster shells. The person who was leading that exploration just put me to work. We started with discarded oyster shells that were open, fired them, and then ground them down into tiny pieces over multiple levels of sifting the smaller material out. Then we ended up tumbling the material to create a paste. And so the oyster shells became – we mixed them with water, and now it created this slurry. The goal is to try to put the material into the clay 3D printer so that overlaps with what I was doing before, understanding the design process for that printer, specifically. We haven’t done that yet, but we’ll see what happens.
GK: [0:09:22] Is that happening later today?
DM: [0:09:23] It is, yeah.
GK: [0:09:25] Wow. That’s so cool. So, are those kinds of material explorations happening for you at New Balance?
DM: [0:09:38] Yeah. We do have an entire team devoted to sustainable materials and sustainable innovation in materials. Even though I’m not directly leading the charge on that, I’m hoping to bring back some learnings and share that with the team. I’d be curious to hear if anyone’s ever worked with oyster shells before. I know there’s been a lot of natural dye experiments and algae experiments. It’ll be really cool to make those connections and see if this could be interesting or useful.
GK: [0:10:19] Within the structure at New Balance, is there a way for you to feel like you can share what happened here?
DM: [0:10:30] Oh yeah, that’ll be a huge component, I think. There’s so much information that I’m gathering and trying to document, so I’ll definitely be sharing that with my core team and also extended teams, such as the Sustainable Innovation Team in hopes to make these connections and spark new ideas.
GK: [0:10:54] Wow. It’s amazing that it’s been – what? – a week that you’ve been here.
DM: [0:11:00] Yeah. Since Saturday evening.
GK: [0:11:05] That’s incredible. So in this short little block of time – because I think one of the things we’re trying to do is capture what is happening at Haystack Labs, how it is this really different kind of synergy. To that end, what was the process of arrival? What do you feel like you’ve accomplished or gained in that amount of time, thinking about arriving here and then what you’re leaving with?
DM: [0:11:44] Yeah. The real accomplishment is creating these connections in hopes of continuing the conversations and the projects, potentially. I have a lot of things in my mind that I want to continue working on. I also had the privilege of working with the most amazing ceramic artist [Timea Tihanyi], who’s been doing ceramic 3D printing for a long time. So, she asked me for help with my workflow – the image workflow to 3D object for her workshop that she’s teaching. It’ll be great to have that tool that could potentially aid other designers. So, things like that, where – how can we help each other and push the design process? I’m hoping to definitely keep in touch and keep the conversations going that started here. Obviously, there’s amazing work, the physical work, that has come out of it, too, which is really inspiring all around. The new technologies that have been developed and people writing software for certain things is also really amazing to see in such a short amount of time.
GK [0:13:18] So, it sounds like you have – are you actually coding with that computational programming?
DM: [0:13:26] I do a little bit of coding, but just scratching the surface. The tools that we use at New Balance and the ones I’ve used here are predominantly Rhino and Grasshopper. It’s a 3D modeling software, and Grasshopper is a free plug-in for that software where you can plug and play with visual blocks of code. It’s very designer-friendly; it’s meant to be approachable if you don’t really know how to code. That was my intro into using these types of tools.
GK: [0:14:00] Cool. So you have that technical side in your work, and it’s pretty creative, too, it sounds like.
DM: [0:14:07] Yeah, definitely. And I do have – just a little bit about my background. I am a trained architect, so that’s what I went to school for, and I practiced architecture for about eight years. I was really embedded in that world. Over the course of that time, I became interested in products and footwear and ended up shifting tracks. So I went into the industry not really knowing anything about footwear but knowing how to design buildings and the design process. I think even though it’s a completely different end result, that set me up well for learning new tools and the footwear industry.
GK: [0:14:56] Do you think you want to come back to Haystack Labs?
DM: [0:15:03] Absolutely. A hundred percent. No hesitation. It’s really unlike anything I’ve ever been a part of. It seems like something special is going on here. I think that’ll become more evident each year, and with the wide variety of different types of artists and technologists that come. So yeah, absolutely.
GK: [0:15:33] Yeah, that’s great. Is there anything that I didn’t ask you about because I don’t know about it?
DM: [0:15:38] [laughter]I think you covered a lot of it. Yeah.
GK: [0:15:44] Okay, cool. Thank you so much. It’s great. I honestly didn’t know that much about the footwear design world, so that’s amazing.
DM: [0:15:56] [laughter] Yeah. Thank you!
This interview features Dana Maringo, a computational designer working at New Balance with expertise in performance footwear and data-driven designs. Maringo discusses her experience at Haystack Labs, where she collaborated on projects involving AI-generated designs and material explorations. She shares insights into the intersection of technology, art, and design at the Labs and highlights the valuable connections she’s made. The interview provides an overview of her work at New Balance, the tools and software she uses, and sheds light on her creative and technical roles.